Abstract
Marking and engraving on PPS (polyphenylene sulfide) is very difficult because it can withstand high temperatures when heated with a laser. Recent advancements in colorant technology, laser-specific carbon blacks, and fiber lasers enable high-contrast, light-colored, scratch-resistant marking of black glass-filled PPS, and certified by Yellow Card. This significant advancement enables the marking and micro-marking of data matrices, barcodes, QR codes, and unique part identification across multiple sectors, including automotive, aerospace/NASA MIL electronics, pumps and valves, appliances, and more. The setup and optics of ytterbium fiber lasers require precision to achieve robust, scratch-resistant markings.
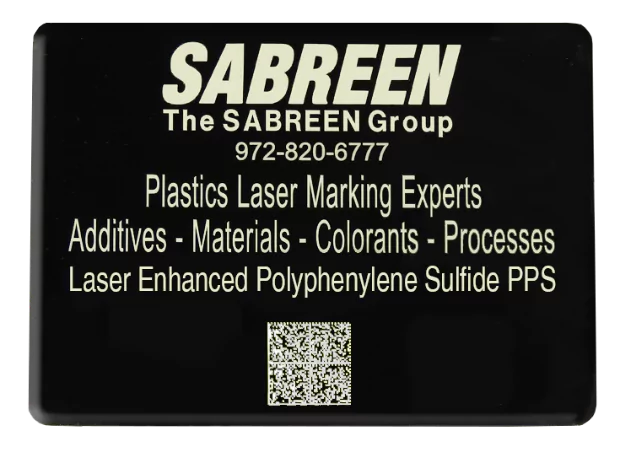
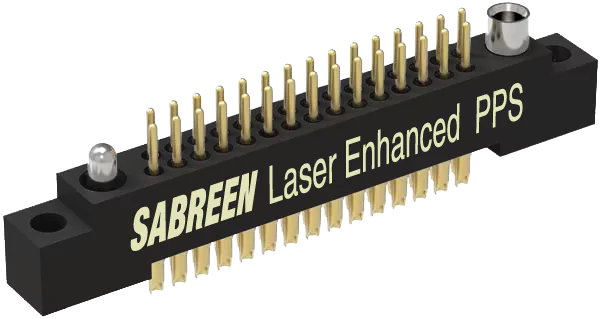
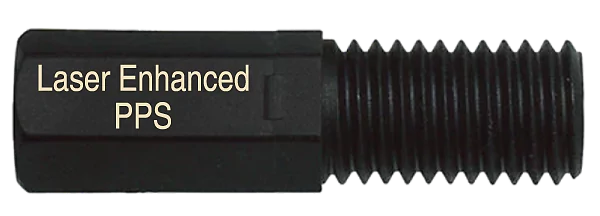
Optimal laser marking. To create scratch-resistant, high-contrast, light-colored markings on black glass-filled PPS, MOPA Ytterbium fiber lasers are the best choice because they can precisely control pulse width and focused power density. This precision allows for better control of the surface chemical foaming process at a near-infrared wavelength of 1060-1070nm. The best pulse duration is between 20 and 40 nanoseconds, with a pulse frequency over 100 kilohertz. A precise laser setup is necessary to control the surface temperature (rise and fall times); otherwise, the marking can easily be scratched off.
To achieve high-quality laser marking on glass-filled polymers, including PPS, requires robust injection molding and dispersion/distribution of laser optimized colorants and precompounded materials. The addition of glass fibers can deleteriously affect molding processes, which in turn affects the quality of laser marking. Resin-rich part surfaces are necessary to achieve robust marking. Surfaces rich in glass fiber will produce inferior marking results.
Polyphenylene Sulfide (PPS)
Polyphenylene Sulfide (PPS) is a high-temperature, semi-crystalline engineering thermoplastic. Within the industry, PPS is known as THE plastic that performs like metal. The properties of PPS, similar to other high-temperature performance plastics including PEEK and LCP, depend on its crystallization behavior. Two distinct forms of PPS are sold: “Branched” molecular structure and “Linear”. Among the most recognizable brands are Celanese Fortron® Solvay Ryton®, SABIC Supec, Toray Torelina, and DIC PPS. The branched version tends to be more rigid. The linear usually offers better mechanical and flexural strength, as well as higher melt stability. Linear PPS also has fewer ionic impurities. Glass-filled fibers (30 percent and 40 percent) and glass fiber/mineral mixtures to standard PPS allow for specialized and demanding applications. Electronics manufacturers commonly select 40 percent glass-filled PPS for insulation and connector products.
To achieve a fully crystalline state, mold temperatures of at least 275 to 300 degrees Fahrenheit are required. When PPS is molded below 275 degrees Fahrenheit, the moldings are amorphous, or semi crystalline, and remain in this state until they are exposed to higher service temperatures. If the service temperature exceeds the molding temperature, the parts will become more crystalline, resulting in dimensional and property changes.
Materials used to make fiberglass are silica, limestone and soda ash. Silica is the main material used to form the glass while soda ash and limestone are used to lower the melting temperature. “Glass emergence” is a serious surface defect that commonly affects fiberglass-filled injection molded products. The exposure of glass fibers causes a glass fiber-rich surface. Excess glass forms on the surface during plastic melt filling and molding. After condensation and molding, white marks appear on the surface. Molded part surfaces must be “resin-rich” in order to produce high quality marking, whereby the energy from the laser interacts with the polymer matrix. Conversely, glass fiber-rich surfaces mark poorly, and the issue gets worse with higher fiber content. Fiberglass itself is not a good absorber of near-IR (NIR) laser light.
Industrial Fiber Lasers
Nanosecond Ytterbium fiber lasers (MOPA and Fixed pulse) are ideal for marking, engraving, and etching plastics due to their superior beam quality (M2) and high brightness “radiance”. They can focus to a small spot size (less than 20 microns), resulting in high energy density. One significant advantage of using MOPA (Master Oscillator Power Amplifier) lasers is ability to fine tune the pulse width. Laser irradiance (W/cm2) and fluence (J/cm2) are important parameters in plastic marking. Irradiance is essentially the intensity of the laser beam which is a function of the focused spot size. Fluence determines the amount of energy that is transferred to the material surface. If the fluence is too low, the material may not be affected at all. If it’s too high, the material can be damaged excessively, beyond the desired marking effect.
Laser pulse repetition rate and peak power density are critical in forming the mark and achieving the optimal contrast and speed. The arithmetic curves of power versus pulse repetition rate are inversely proportional. High peak power at low frequency increases the surface temperature rapidly, vaporizing the material while conducting minimal heat into the substrate. As the pulse repetition increases, lower peak power produces minimal vaporization but conducts more heat.
Contact The SABREEN Group to learn more…bring us your toughest laser marking challenges!
Scott R. Sabreen is founder and president of The Sabreen Group, Inc., which is an engineering company specializing in secondary plastics manufacturing processes – surface pretreatments, bonding decorating and finishing, laser marking and product security. He has been developing new technologies and solving manufacturing problems for over 30 years. Sabreen can be contacted at 972.820.6777 or by visiting www.sabreen.com or https://sabreen.com/solutions/plastics-laser-marking/