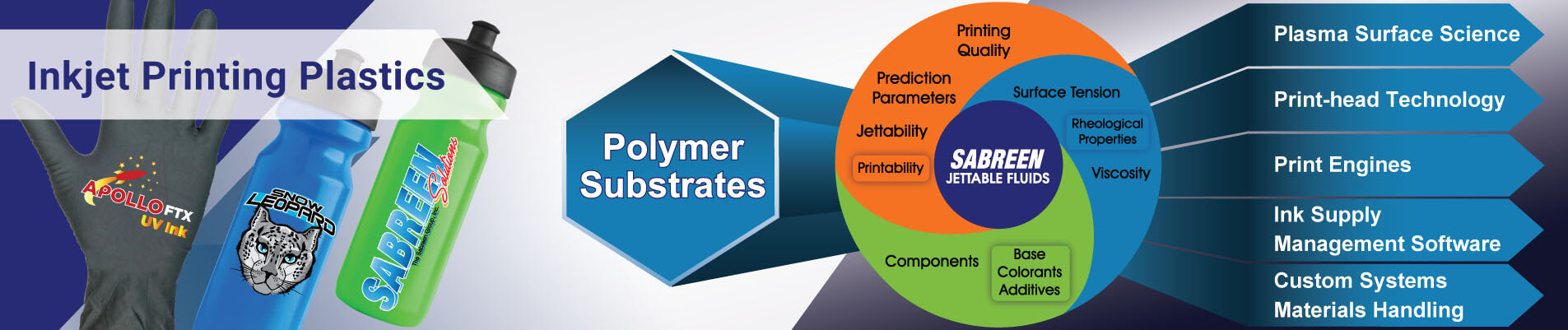
Total Solutions for Industrial Inkjet Printing onto Plastics
Wearables, Flexible Products, Mass Customization, Ad Specialties
Piezoelectric drop-on-demand UV LED inkjet printing onto polymers and flexible substrates is more complex and delicate than traditional analog printing. Drop-on-demand inkjet technology requires the nozzles to fire precisely sized drops with exact accuracy. High-quality inkjet printing systems must simultaneously integrate printheads, fluids, electronic controllers, pretreatment and cure. All items must work seamlessly together to produce the intended results.
There are three main input process parameters: 1) polymer substrate, 2) inkjet printer and 3) ink chemistry and substrate surface compatibility. All elements must be precise and stable to achieve excellent print quality. Changing any one of these parameters has an unbalancing effect requiring modifications to the others. Printing on 3-dimensional and contoured geometries is further complicated as there are relatively few OEM printer/ printhead choices. Each OEM limits certified inks developed for a limited range. A thorough understanding of the intricacies of inkjet printing and surface science enables unprecedented capabilities and results.
SABREEN has recently developed and commercialized UVLED inks and inkjet printing processes for customization of flexible plastic and rubber products which stretch greater than 100-percent. Products include therapeutic exercise bands, swimming caps, hygienic wearables and more. Independent Toxicology analysis conforms to CAL Prop 65, US Toxicity Risk Assessment and ASTM D 4236 (LHAMA – 16 CFR 1500.14).
Our Inkjet Printing Process uses High-Quality Inks and Advanced Printing Technology to Ensure Vibrant, Long-Lasting Images on all Types of Plastics.
For inkjet printing, adhesion is critical. Variables affecting adhesion include polymer material (including colorants, fillers and additives), molding process, surface conditions, texture, and storage & handling. It’s important for design and manufacturing engineers to select the optimal thermoplastic that achieves field performance criteria and is easily printed. Protective clear coatings (topcoat) allows extended chemical/abrasion resistant protection such as hot water dishwasher cleaning (exceeding 500 consecutive cycles). These coatings are applied on top of pigmented inks in either inkjet fluid or spray atomization.
Thermoplastics are divided into two subcategories, amorphous and crystalline. the very long, chain-like molecules are held together by relatively weak Vander Waals forces. Generally, amorphous polymers possess better adhesion properties than crystalline. The term amorphous means to have no defined shape, or an easily altered shape. Crystalline, implies that there is a regular, defined pattern to the molecular aggregates. Amorphous resins such as ABS, styrene and polycarbonate exhibit random, spaghetti-like structure. As heat is applied, they soften and do not have sharply defined melting temperature.
Crystalline resins such as polyolefins, PET and nylon have orderly pattern, like coiled spring just as metal spring dampen vibration, so crystalline materials. They have well defined melting temperature. In a polymer, these two states coexist, with adjacent sections polymers packing into tight crystalline bundles held together by secondary attraction forces, while other sections of the same molecules are unable to physically move into the crystalline lattice and remain amorphous. See Figure 2.
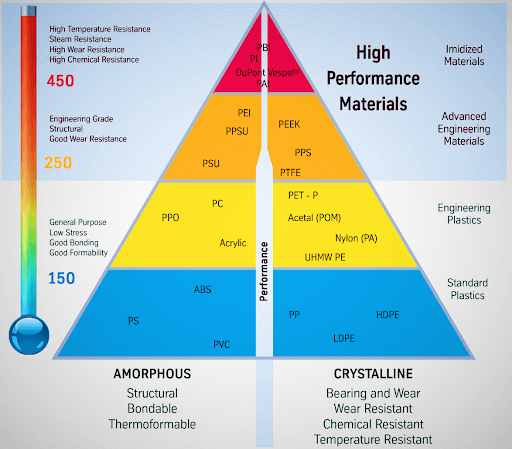
Selection of Thermoplastics – Process Compatibility
For inkjet printing to be successful the elevated temperature ink must easily jet from the printhead on, appropriately interact with substrate and achieve strong adhesion. This intimate contact is termed “wetting” or “wetting out” the surface and refers to the inks ability to spread over the surface. However, most polymer surfaces are naturally hydrophobic, and resist being wetted. Characteristically, these plastics are chemically inert, nonporous surfaces with low surface energy which makes printing adhesion nearly impossible. Surface energy is the excess energy that exists at the surface (as opposed to the bulk) of a solid.
Primary molding processing is critical to achieving the stated properties of the polymer material. Incorporating the proper plasma surface pretreatment in conjunction with surface texture and good manufacturing practices will resolve most, if not all adhesion and wetting problems. Selecting the best thermoplastic for any given application is not easy. Part designers often seek chemical bulk material and surface properties that are often very difficult to print. Let’s examine application examples which demonstrate the critical balance between polymer selection and ease of printability.
Color inkjet printing onto polyamide (nylon) is one of the most sought-after applications. The chemical composition of Nylon gives it a high melting point, making it an excellent alternative to metal components in high-temperature environments, like car engines and other types of high-friction machinery. Like other thermoplastic materials, nylon plastic turns to liquid at its melting point rather than burning, meaning it can be melted down and remolded or recycled. Nylon material also doesn’t heat up easily when used in high friction applications. However, inkjet inks do not adhere readily to nylon (or most low-surface-energy polymers) without specialized ink and pretreatment. This is due, in part, to its hydrophobic properties. Reference Figure 3.
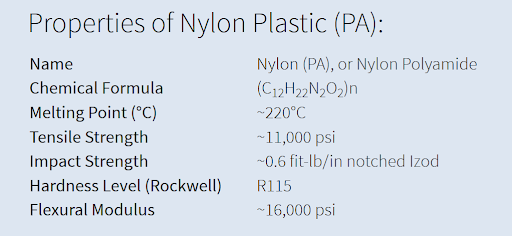
First and foremost, ensure that nylon materials are properly dried and processed to achieve dry-as-molded properties. Resin manufacturers chemically produce their products differently, which can affect adhesion performance. Evaluate alternative suppliers by resin/grade, and note the differences between Nylon 6 and Nylon 66 (Nylon 11 & 12). Unlike Nylon 6, Nylon 66 is comprised of two monomers, Hexamethylenediamine, and adipic acid, each providing six carbon atoms, hence the 66 name. The material is more crystalline in nature than Nylon 6, which improves stiffness and tensile and flexural modulus.
Nylon 6 will absorb slightly more moisture than Nylon 66. Following molding before secondary operations, products should be packed preferably in polyester bags and not polybags. Low-molecular-weight species found in polybags migrate to the surface, causing cross-contamination issues. Length of time in storage and temperature also affect adhesion performance. Print as soon as possible after molding.
If printing problems cannot be resolved, consider using an alternative plastic that may have similar properties and is easier to print or laser mark. This point emphasizes the criticality for both designers and manufacturing engineers to develop the product specifications. Polypropylene and & high-density polyethylene (HDPE) are less sensitive to molding, material & printing issues and less expensive. HDPE is the easiest of the three to print because its more thermodynamically stable. Reference Figure 4.
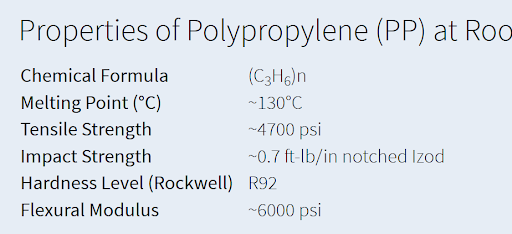
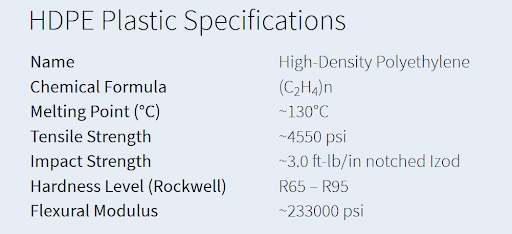
Inkjet inks have low viscosity and low surface tension, which create adhesion bonding challenges on many polymeric substrates such as acetals, polyolefins, and polyurethanes. These types of chemically inert plastics are hydrophobic and not naturally wettable. Consider a single liquid fluid droplet on a flat solid surface at rest (equilibrium). The angle formed by the solid surface and the tangent line to the upper surface at the end point is called the contact angle; it is the angle (x) between the tangent line at the contact point and the horizontal line of the solid surface. Reference Figure 2.
The bubble/droplet shape is due to the molecular forces by which all liquids, through contraction of the surface, tend to form the contained volume into a shape having the least surface area. The intermolecular forces that contract the surface are termed “surface tension”.
Surface tension, a measurement of surface energy, is expressed in dynes/cm. The higher the surface energy of the solid substrate relative to the surface tension of a liquid (water, printing inks, adhesives/encapsulation, coatings, etc.), the better will be its “wettability,” and the smaller will be the contact angle (Figure 2).
As a general rule, acceptable bonding adhesion is achieved when the surface energy of a substrate is approximately 8 to 10 dynes/cm greater than the surface tension of the liquid.
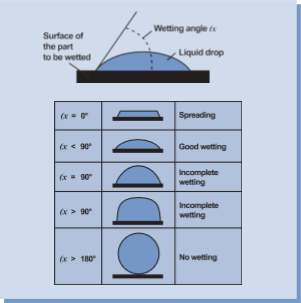
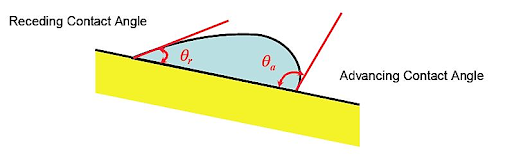
In reality, fluids and contact angles are dynamic, not static. Reference Figure 3. The dynamic contact angle (DCA) is most important. When a droplet is attached to a solid surface, and the solid surface is tilted, the droplet will lunge forward and slide downward. The angles formed are termed, respectively, the advancing angle (θa) and the receding angle (θr).
Contact angles generally are considered to be affected by both changes in surface chemistry and changes in surface topography. The advancing contact angle is most sensitive to the low-energy (unmodified) components of the substrate surface, while the receding angle is more sensitive to the high-energy, oxidized groups introduced by surface pretreatments. Thus, the receding angle actually is the measurement most characteristic of the modified component of the surface following pretreatments, as measured using dyne solutions. Therefore, it is important to measure both the advancing and receding contact angles on all surface-modified materials.
Material purity also is an important factor. The shelf life of treated plastics depends on the type of resin, formulation and the ambient environment of the storage area. Shelf life of treated products is limited by the presence of materials such as antioxidants, plasticizers, slip and antistatic agents, colorants and pigments, stabilizers, etc. Exposure of treated surfaces to elevated temperatures increases molecular chain mobility – the higher the chain mobility the faster the aging of the treatment. Polymer chain mobility in treated materials causes the bonding sites created by the treatment to move away from the surface. These components may eventually migrate to the polymer surface. Therefore, it is recommended to bond, coat, paint, print or decorate the product as soon as possible after pretreatment.
UV inks use only pigment colorants, but the range is broad and not a serious limitation. Formulating and ink-making developments enable manufacturers to offer white (W), which is especially useful as a base on dark-colored substrates or as a background on clear. Inkjet primary colors – cyan, magenta, yellow and black (CMYK) together – offer a large color gamut because ink layers can be thick. However, being based on pigments, they are at least partially opaque and they mask colors below. The intensity does not fully translate into the secondary colors, which excludes a number of Pantone colors popular with major brands.
Analog printing uses specifically formulated spot colors. They could be available in this market, especially with 6-, 8- and 10-printhead machines, but they are not popular because it is far more difficult to change out a spot color in an inkjet printer than in flexographic or screen printing. This also conflicts with the ability of digital to switch jobs with consecutive images. An alternative is to employ extended gamut ink sets with intense inks of hue intermediate between CM and Y. Red, green and blue (RGB), or orange, green and violet (OGV) are used in label and advertising printing to extend the gamut and cover most bright, specified, intense brand colors. These colors also can be custom formulated for three-dimensional plastic products.
Reproducing light colors, especially flesh tones, is a consistent difficulty for UV-cure inkjet printing. Even the smallest droplets of CMK, now as little as 4 picoliter, are too large for photo-realism. However, if a secondary set of light magenta (lm) and light cyan (lc) are included, the artifacts of individual dots are eliminated. The option of CMYKlclmW is available to this market from the printer OEMs.