Polyethylene (PE) is one of the most widely utilized polymers and is classified by its density and branching. The type of PE has a significant impact on the ease or difficulty of secondary operations. The most common types are LDPE, HDPE & Cross-linked. PE products are difficult to bond and decorate due to their chemical, physical & hydrophobic surface properties. This article discusses state-of-the-art secondary processes for achieving superior bonding, coating, inkjet printing & laser marking on PE.
The first step in achieving robust secondary operations is understanding the differences between the types of PE – branched, linear & cross-linked. While PE is not hygroscopic it’s non-wettable, and low surface free energy that can be further lowered by the presence of low molecular weight oxidized materials. Inorganic mixed metal oxide pigments can affect the degree of crystallinity and the speed of crystallization that determine the final properties of a plastic part. Primary molding operations and cooling rate are critical in terms of determining interfacial adhesion between polyolefins.
Polyethylene
PE is a variable crystalline thermoplastic belonging to polyolefin family and is classified by its density and branching. Major uses include packaging applications, automotive, electrical, consumer goods, fibers & textiles, and pipes & fittings. PE mechanical properties depend significantly on variables such as the extent and type of branching, the crystal structure, and the molecular weight. PE is made by addition or radical polymerization of ethylene (olefin) monomers.
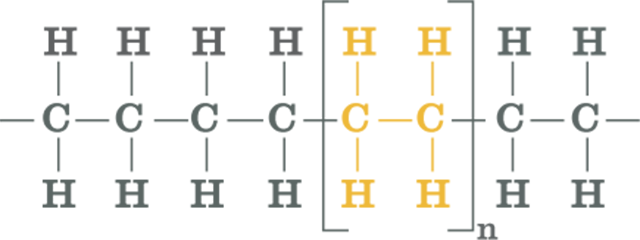
A major attribute of PE is its ability to be easily altered during processing to give a variety of forms that differ based on polymer chain length, density, and crystallinity. These characteristics allow PE products to be tailored for a range of uses. The most common types of polyethylene are listed below.
Branched Versions
- Low-density polyethylene (LDPE)
- Linear low-density polyethylene (LLDPE)
- Linear Versions
High-density polyethylene (HDPE)
- Ultra-high-molecular-weight polyethylene (UHMWPE)
- Cross-linked polyethylene (PEX or XLPE)
PE is also available in other types, such as but not limited to: Medium-density polyethylene (MDPE), Ultra low-density polyethylene (ULDPE), High-molecular-weight polyethylene (HMWPE), Metallocene polyethylene (mPE) and Chlorinated polyethylene (CPE).
Differences Between HDPE and LDPE
The type of PE selected by designers strongly determines the ease or difficulty of secondary operations. LDPE and HDPE share many characteristics, but their fundamentally different internal compositions result in many differences. The polymer chains that make up both materials are branched in LDPE, whereas in HDPE the polymers have a more crystalline structure. HDPE is more susceptible to environmental stress-cracking. Differences in polymer organization leads to distinct characteristics in each material. A study published in the Journal of Applied Polymer Science evaluating thermal properties found that LDPE was thermally less stable than HDPE1. Work conducted by The Sabreen Group supports this conclusion that HDPE is more thermally stable than LDPE and is often easier to bond and laser mark².
Adhesion
Strong adhesion bonding is a prerequisite for many secondary processes. Semi-crystalline PE is difficult to wet due to its hydrophobic properties and low surface free energy, which can be further lowered by the presence of LMWOM such as mold release, antioxidants, plasticizers, slip and antistatic agents, colorants & pigments, and stabilizers. In addition to the chemical composition of the surface, texture, porosity, and any LMWOM contamination or barriers that coat the surface of the substrate which bloom to the surface, or contaminants from handling can affect the liquid’s ability to flow and achieve intimate contact. Surface cleanliness is critical. In addition to chemical adhesion, surface roughness can increase mechanical adhesion. Pretreatment is usually required for PE bonding components. Plasma pretreatment is a preferred method.
Even if cleaned of contaminants, PE surfaces may resist being wetted by a liquid (adhesive, coating, or ink). This is due to a phenomenon known as surface energy. Surface energy is the excess energy that exists at the surface of a solid, as opposed to the bulk. This excess energy exists because molecules at the surface cannot interact with as many like neighboring molecules, as molecules in the bulk are able to do. Consequently, they have excess interaction energy.
Plasma Pretreatment
What’s New? Atmospheric Plasma with variable power control up to 500W and larger treatment areas manufactured by industry leader 3DT LLC PlasmaDyne Pro. These advancements allow precise power control of high purity plasma ionization for inline & automated (robotic) systems.
Gas-phase “glow-discharge” plasma surface (modification) oxidation is highly effective in solving adhesion problems of non-polar, chemically inert, hydrophobic polymer surfaces. Commonly known processes are electrical atmospheric plasma, flame plasma, Pyrosil®, electrical corona discharge, electrical air plasma, low-pressure RF cold gas, and UV/ozone. All of these processes add chemical functionality in addition to increasing surface energy. Reference online technical article “Plasma Surface Pretreatments of Polymers for Improved Adhesion Bonding”, Plastics Decorating Magazine 2018.
This paper examines three plasma pretreatment processes that are well suited for inline or secondary treatment of PE components, and all polyolefins – 1) electrical atmospheric plasma, 2) flame plasma, and 3) Pyrosil®. Photo 1. The selection of which process is best for any application depends on many factors including polymer type, part thickness, and geometry.
Atmospheric Plasma
Atmospheric plasma or electrical blown ion plasma utilizes a nozzle electrode, powered by an electrical generator and step-up transformer, and high-pressurized air in which intense plasma is generated within the treatment head and streams outward. Ozone formation is negligible. This pretreatment process is near potential-free (for treatment of conductive materials including metals) and can remove dirt, debris, and most hydrocarbons from the substrate. New research indicates fine etching of the surface can create new topographies for increased mechanical bonding.
Flame Plasma Treatment
Flame plasma treatment uses the highly reactive species present in the combustion of air and hydrocarbon gas to create the plasma. While flame treatment is exothermic, heat does not create the chemical functionality and improved surface wetting. Flaming will remove dirt, debris, and most hydrocarbons from the substrate. Flame treatment can impart higher wetting, oxidation, and shelf life than electrical pretreatments due to its relatively shallower depth of treatment from the surface, 5 to 10 nm. Studies show flame plasma on polyolefins produces the longest post-treatment shelf life due to its relatively shallower depth of treatment, an advantage for products. Ozone is not produced. When procuring flame treatment burners, ribbon burners provide greater flame uniformity with zero balanced regulators. Flaming with propane gas is ideal for treating PE and polyolefin durable parts.
CCVD Pyrosil®
Not to be confused with Flame plasma, Pyrosil® treatment is a surface modification technique that deposits an amorphous silicon dioxide (SiO2) layer on a substrate surface via Combustion Chemical Vapor Deposition (CCVD). By means of flame-pyrolysis, a thin layer (5 – 100 nm) of highly reactive and hydrophobic silicone oxide can be achieved on the substrate. Consequently, a defined hydrophilic surface is built due to the high density of Si-OH groups on the surface of the deposited SiO2 particles and nanoscale roughness. Pyrosil® (pinkish color flame) and traditional flame plasma (bluish color flame) have process similarities however the flame chemistry and surface functionality mechanisms are different. The main difference is that Pyrosil® produces SiO2, flame treatment does not.
Single-pass UV LED Inkjet Printing
What’s New? Single-pass UV LED inkjet printing systems for flexible & rigid PE/polyolefins, incorporating toxicity-safe and biocompatibility certified inks. Photo 2.
The significant advantage of full-color single-pass printing, versus scanning, is faster speed and increased productivity. Many of the safety issues with UV inks have been rectified. A new UV LED ink, Apollo FTX Ink Series† has been qualified in specific applications to be safe for adults and children, contact with human skin, per ASTM D 4236 (LHAMA – 16 CFR 1500.14) and biocompatibility tested.
The ink properties possess excellent wetting, adhesion, and intermolecular adhesion between white ink (base layer) and CMYK++ colors. This ink has a high consistent flow and exit contact angle of the ink leaving the nozzle yielding uniform jet break-up. The chemistry is precisely matched to specific UV LED cure profiles ensuring strong final cure properties and aesthetics, not under-cure (tacky) or over-cure (brittle).
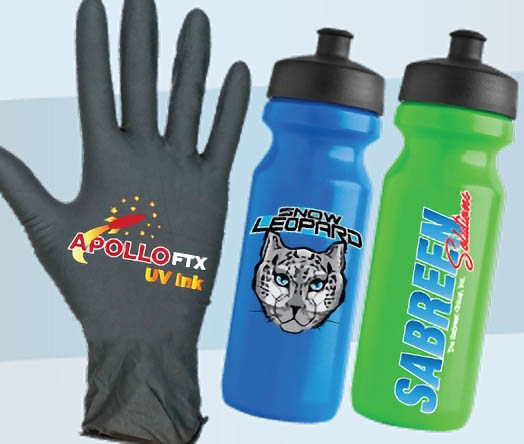
Coating and Painting
What’s New? UV LED cured coatings with decorative effect pigments and weatherability on PE, including recycled plastics. Photo 3.
UV cured coatings offer the best combination of fast-drying/curing time and performance of any coating technology for plastic. Curing can typically be achieved in as little as 3-10 seconds. Once cured, plastic products decorated with UV curable coatings are immediately ready for packaging.
UV cure coatings excel in toughness and chemical resistance and can be formulated to achieve long-term exterior durability. Mercury vapor lamps are the most commonly used UV source for curing. Arc style lamps are more cost-effective to purchase but require warm-up time and produce considerable heat.
Microwave-generated lamps are more expensive than arc lamps but are ready to use within seconds of being turned on, produce less heat, and have longer bulb life. LED UV lamps has emerged as a competing technology offering instant on/off capability with very low energy usage and extremely low heat generation. UV coatings are easily sprayed atomized with HVLP, manually or robotics.
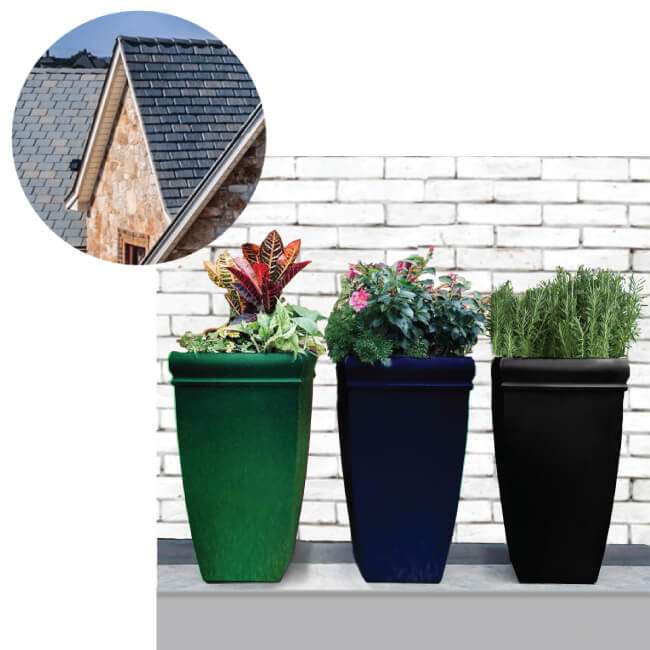
Fiber Laser Marking
What’s New? In-direct food contact and medical/FDA compliant laser enhancing additives, and MOPA Ytterbium fiber lasers.
New chemical additives produce superior marking contrast (opaque white & jet black on PE) and do not affect polymer clarity, spectral transmission, or base physical properties. Laser marking PE without additives produces practically illegible marks, similar to many thermoplastics. Since most polymers do not possess absorption properties at 1060 to 1070 nm, experts utilize additives, fillers, pigments, and dyes that enhance the absorption of laser energy for localized color changes. Studies with PE suggest that thermal stability and heat degradation properties are critical pathway mechanisms. Reference Figure 1. Further, HDPE produces superior quality versus LDPE and LLDPE and polyolefins using near-IR lasers.
Thermal gravimetric analyses (TGA) from ambient to 1000°C of two HDPE samples showing differences in thermal degradation temperatures. HDPE B will mark more easily and faster than HDPE A.
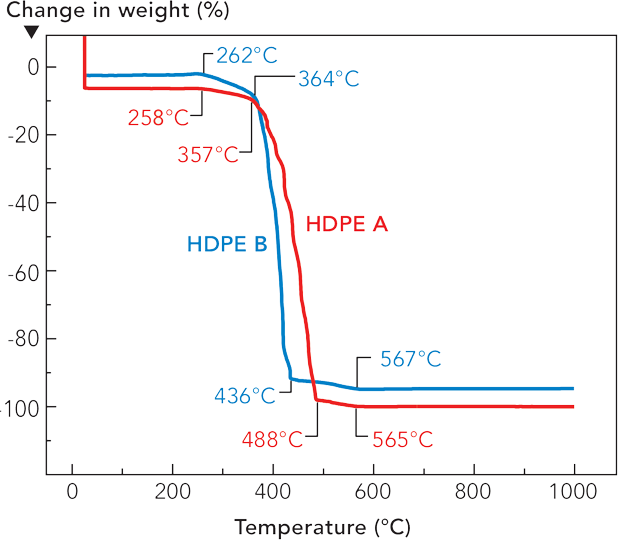
Typical loading concentration level by weight in the final part typically ranges between 0.01 and 3.0%. Both granulate and powder forms can be blended into precompounded color material or color concentrate. Laser additives are cost-saving and demonstrate 20% and faster marking speeds versus non-optimized materials.
Ytterbium fiber lasers are among the most significant advancements for marking polymers. Q-switched fiber lasers, typically with 100 to 120 ns pulse width, are used for some polymer marking applications, but their repetition rate is limited to around 80kHz because of the inherent constraint of Q-switching technology. Directly modulated MOPA fiber lasers can operate at repetition rates of up to 500kHz at nanosecond pulse widths (20 ns to 70 ns for PE), making temporal pulse shape waveguide ideal for laser enhanced polymers. Photo 4.
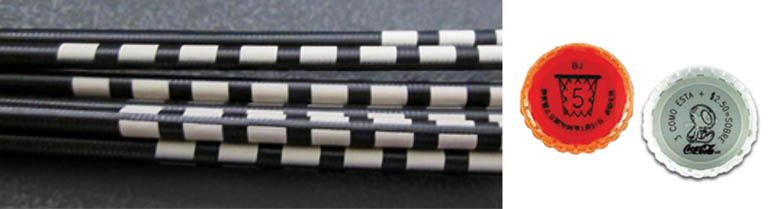
Conclusion
Advanced technologies provide new solutions for decorating & finishing polyethylene products. Secondary processes examined are bonding, coating, inkjet printing & laser marking. The type of PE has a significant impact on the ease or difficulty of manufacturing. PE is difficult to bond and decorate due to its bulk and hydrophobic surface properties. Molding operations including cooling rate is important in terms of determining interfacial adhesion. HDPE is generally easier to bond and laser mark than LDPE due to differences in thermal stability. Single-pass UV LED inkjet printing systems for flexible & rigid PE/polyolefins, incorporating toxicity-safe and biocompatibility-certified inks are among the most exciting new technologies.
References
- 2002 Wiley Periodicals, Inc. J Appl Polymer Sci 86: 764–772, 2002.
- Sabreen, S. “Thermoplastic Materials for UV Inkjet and Laser Marking”, Plastics Decorating Magazine 2019.
†Apollo FTX Ink series is available for purchase. Contact The Sabreen Group at 972.820.6777 or engineering@sabreen.com
Scott R. Sabreen is the founder and president of The Sabreen Group, Inc., an engineering consulting company specializing in secondary plastics manufacturing processes – surface pretreatments, adhesion bonding, inkjet printing, laser marking, industrial coatings, decorating and finishing, and product security. Sabreen has been developing pioneering technologies and solving manufacturing problems for more than 30 years. He can be contacted at 972.820.6777 or by visiting www.sabreen.com.