This is the first of a two-part series on the most significant technological developments in industrial laser marking of plastics. We’ll examine Ytterbium fiber laser architecture, how they work and the major performance factors that determine marking quality. Part 2 examines new solutions that use MOPA marking lasers, polymers and FDA compliant additives to achieve superior marking contrast quality, custom colors and fast speed, including in line laser marking.
The Rise of MOPA Fiber Marking Lasers
Q-switched nanosecond Ytterbium fiber lasers have been used for marking plastics since their invention over 30 years ago. Advantages offered by these lasers include fiber delivery, smaller footprint, lower maintenance, and lower price. Fiber lasers can have better beam quality and brightness than their arc-lamp Nd: YAG laser predecessors, when manufacturers use “multi-mode” output instead of “low-order” mode or “TEM00” transverse electromagnetic mode.
Fiber marking lasers typically have a pulse energy of 1 mJ of energy per individual pulse. Their low cost and convenient fiber delivery quickly made them attractive for laser marking applications. The fundamental design of Q-switched fiber laser has not changed much over time and these lasers are still popular for many plastic marking applications. The designs are stable, but the interconnected laser parameters impose limitations on process optimization. Nearly 25 years ago, scientists at SPI Lasers (now TRUMPF Lasers) were working quickly on the next generation of fiber marking lasers.
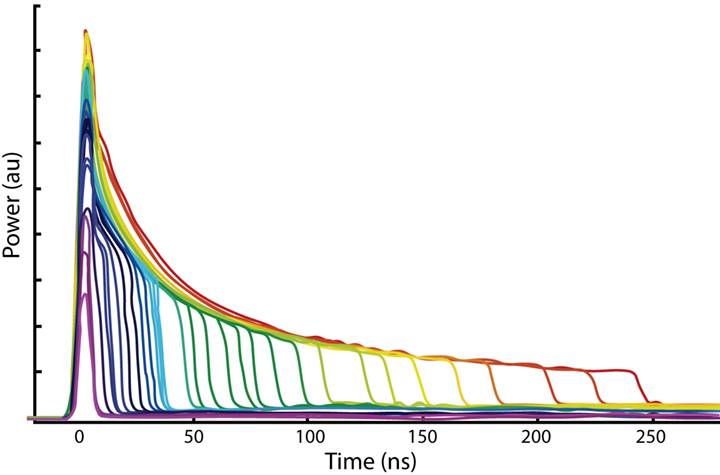
The emergence of MOPA (Master Oscillator Power Amplifier) designed nanosecond Ytterbium fiber lasers is one of the most significant advancements in laser plastic marking. An industry-changing laser design now provides pulsed energy differently than traditional mirror/Q-switch cavities. The design utilizes “waveforms” as a laser tool for quick processing and fine pulse control. Graph 1 shows the 40 different colored waveform pulses from the TRUMPF TruPulse Nano MOPA fiber lasers. Each color in the graph displays a distinct MOPA pulse waveform that can be used to balance the fluence and irradiance to optimize plastic marking results. As with many competing technologies, there often is confusion and unintended misrepresentation of important terminology and distinctive factors. This article articulates the science and terminology of fiber lasers so that readers and buyers of lasers can make informed decisions.
A MOPA fiber laser, Diagram 1 amplifies a modulated low-power telecom-quality laser diode to produce precise high-power laser pulses. By using an internal pulse generator to modulate the low-power diode, the laser can selectively set, maintain, or adjust the pulse width and resulting pulse energy over a broad pulse modulation rate.

This architecture effectively decouples the laser parameters versus Q-switched and provides greater process optimization and repeatability for better and more consistent marking results. Standard MOPA fiber laser designs can exhibit similar beam quality (M2) variation issues as Q-switched fiber lasers. TRUMPF, a leading fiber laser manufacturer, offers a patented dual-stage GTWave fiber amplifier design that maintains consistent M2 over its specified pulse repetition range. Unlike MOPA fiber lasers, an actively Q-switched fiber laser works by disrupting the gain in the laser cavity, thus allowing gain build-up in the amplifier and high-power laser pulses to be emitted when the disruption is removed. Key parameters in Q switched fiber lasers are tightly coupled.
The diode current can be increased or decreased to change the output power. Increasing the pulse repetition rate should increase the average power, however, this is not the case with Q-switched fiber lasers as the pulse power decreases. Chart 2 shows power and repetition rates as a function of time. The M2 (beam quality) on Q-switched fiber lasers can vary considerably with any change in laser power and pulse repetition rate. Varying the M2 between 1.1 and 1.5 will result in a 2x change in focused power density which can dramatically change marking quality on plastics.
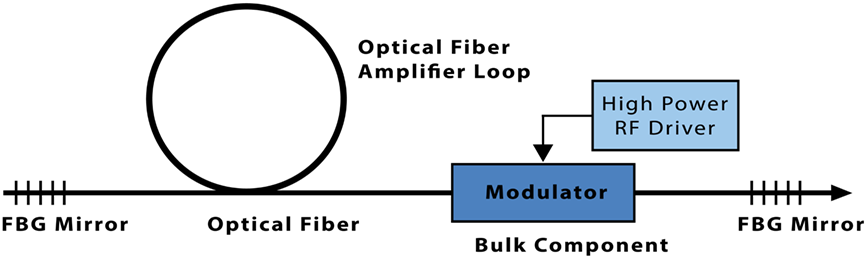
Factors Affecting Laser Marking Quality
Ytterbium fiber lasers operate in the near-infrared (NIR) spectrum having a wavelength of 1060-1070 nm. The functionality of a marking laser is to irradiate the part surface (polymer) with a localized high-energy radiation source (laser). The radiant energy then is absorbed by the material and converted to thermal energy. Thermal energy induces “thermal-chemical” reactions to occur in the material. Beam steered laser markers utilize mirrors that are mounted on high speed computer-controlled galvanometers to direct the laser beam across the surface to be marked. Each galvanometer, one on the Y-axis and one on the X-axis, provides the beam motion within the marking field. The flat-field lens assembly focuses the laser light to achieve high power density on the substrate surface.
Beam Quality
The beam quality factor M2 is a quantification of the focus ability of a beam and is critical to marking performance. The M2 factor of a laser beam limits the degree to which the beam can be focused for a given beam divergence which is limited by the aperture of the focusing lens. M2 = 1 is the ideal Gaussian laser beam. Together with the optical power, the beam quality factor determines the brightness “radiance” of the laser beam. A consistent M2 factor is more important than the value itself, as various applications require different beam modes. A lack of consistency is a common problem with lower-performance lasers resulting in marking variation, appearance and functionality.
Laser Irradiance and Fluence
Laser irradiance and fluence are key parameters in plastic marking. The following is a brief description of how they impact the marking process:
Laser irradiance: Irradiance is the power of the laser per unit area, measured in watts per square centimeter (W/cm2). It is essentially the intensity of the laser beam which is a function of the focused spot size. Focused laser spot size for any given focal length lens and laser wavelength is a function of laser beam divergence. Larger spot size results in lower energy density. High irradiance can lead to rapid heating and vaporization of the material, while low irradiance might not create a visible mark at all. The irradiance affects the speed and quality of the marking process. High irradiance can lead to faster marking, as the material is rapidly heated and vaporized. However, if the irradiance is too high, it can cause damage to the material, such as cracking or excessive burning. On the other hand, low irradiance may result in slow marking speed or no visible mark at all.
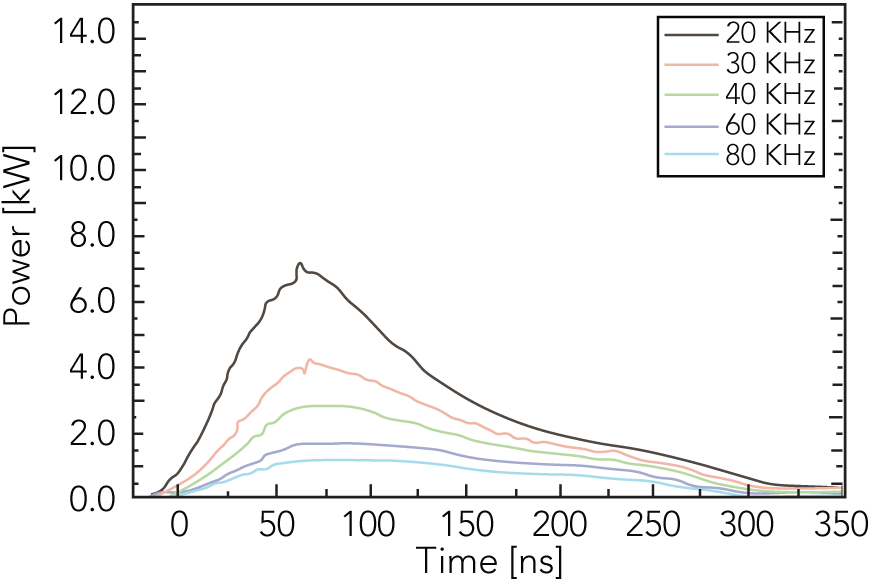
Intensity is influenced by:
- Pulse frequency (Hz, kHz) – pulse repetition rate
- Laser power (watt) – different from power density W/cm2
- Focal spot size – also referred to as focal diameter
- Pulse width – the time between the beginning and the end of an impulse measured in nanoseconds, pico-, or femtoseconds. A factor for controlling energy density, and critical for process optimization. Pulse duration adjustment in MOPA lasers is more flexible than Q-switched (fixed pulse) fiber lasers.
Laser fluence: Fluence is a measure of the laser energy per unit area. It is typically measured in joules per square centimeter (J/cm2). Fluence determines the amount of energy that is transferred to the material surface. If the fluence is too low, the material may not be affected at all. If it’s too high, the material can be damaged excessively, beyond the desired marking effect. The fluence must be at an appropriate level for the specific material being marked. Some materials may require higher fluence to absorb sufficient energy for a visible mark, while others may require lower fluence to avoid damage. The depth of the mark also can be influenced by the fluence; generally, higher fluence leads to deeper marks.
Fluence is influenced by:
- Beam intensity
- Scanner velocity
- Pulse overlap
- Focus beam diameter
Pulse repetition rate and peak power density are critical parameters in forming the mark and achieving the optimal contrast and speed. High peak power at low frequency increases the surface temperature rapidly, vaporizing the material while conducting minimal heat into the substrate. As the pulse repetition increases, a lower peak power produces minimal vaporization but conducts more heat. The arithmetic curves of power versus pulse repetition rate are inversely proportional. Additional contributing factors of marking beam velocity and vector line separation distance determine the marking contrast and quality.
By carefully adjusting and controlling these parameters, laser marking can be used to create precise, high-quality marks on a range of plastic materials. It’s a balance that depends on the material’s properties, the desired mark depth and the required marking speed. Adding laser absorbers to plastic greatly increases the range of markable plastic materials, improves the mark quality, and broadens the process window to insure mark consistency.
All Lasers Are Not Created Equal!
Trumpf Lasers developed the ground-breaking MOPA fiber architecture and industrial marking systems, described in this article, which assure consistent marking results across all lasers. It is critical to distinguish between industrial and low-cost wholesale lasers.
Industrial lasers are superior to cheap wholesale (resellers) hobbyist-type lasers. Industrial lasers can run continuously 24/7 and are equipped with highquality optics, lenses, scan-heads, electronics, and versatile software. Some of the industry’s top manufacturers use realtime remote system monitoring to detect problems before they develop. Cheap lasers have serious problems with erratic marking quality, inexpensive optics and electronics, which causes variations in beam quality and inconsistent marking.
In Part 2 of this article, readers will learn about how advances in plastics material science and nanosecond fiber lasers have made it possible to mark plastics that have been difficult or even impossible to laser mark with high-quality contrast, custom colors and speed that have never been seen before.
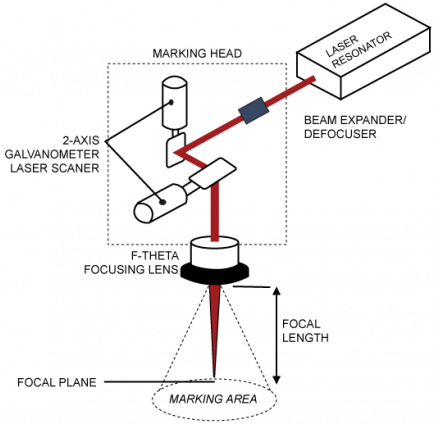
In memoriam: This article is dedicated to Mark Brodsky, a true laser visionary, inventor, colleague and friend.
References
1. Brodsky, M. “Wave Forms: A New Laser Tool,” Optics & Photonics, March 2012
2. “Laser Marking at a Glance Brochure,” TRUMPF Laser
3. Sabreen, S. “Fiber Lasers: Selection and Additives,” Plastics Decorating magazine, November 2017.