PYROSIL® treatment is a combustion chemical vapor deposition (CCVD) process utilized to improve adhesion on surfaces to be bonded. PYROSIL® is a glow-discharge plasma process conducted at ambient conditions, easily integrated inline. Highly effective for pretreating glassware, ceramics, and metals prior to ink printing, the process yields excellent adhesion, scratch and chemical resistance. PYROSIL® is less common in polymer applications due to factors including:
- misunderstanding in its application
- improper equipment and setup
- lack of surface analysis testing
- confusing industry terminology
This article discusses PYROSIL® for improving adhesion on two-dimensional and three-dimensional plastic applications supported by empirical studies.
Many polymers are inherently hydrophobic, low surface energy substrates that do not adhere well to like or dissimilar materials. Surface modification methods are proven to solve most adhesion problems. Traditional methods include electrical (corona) discharge, flame plasma, atmospheric plasma, cold-gas plasma and UV radiation-ozone. Surface oxidation pretreatment of polymeric surfaces introduces polar reactive groups, which improve surface free energy and consequently the wettability and bondability of these surfaces. A newer method, PYROSIL® flame treatment is rapidly emerging as a highly effective process for improving adhesion on tough-to-adhere polymers. SURA Instruments GmbH, Applied Surface Technologies LLC and The Sabreen Group Inc are collaborating to advance PYROSIL® for optimizing adhesion on plastic products.
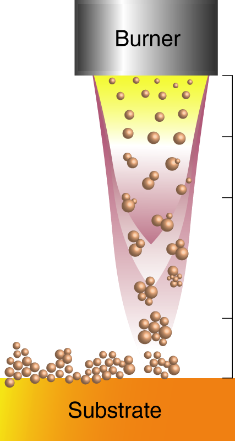
What is PYROSIL®?
PYROSIL® treatment is a surface modification technique that deposits an amorphous silicon dioxide (SiO2) layer on a substrate surface via Combustion Chemical Vapor Deposition (CCVD). SURA Instruments GmbH developed the equipment and processes in the 1980’s that lead to the first successful commercialization of the technology used to increase bonding with adhesives.
By means of flame-pyrolysis, a thin layer (5 – 100 nm) of highly reactive and hydrophobic silicone oxide can be achieved on the substrate. Consequently, a defined hydrophilic surface is built due to the high density of Si-OH groups on the surface of the deposited SiO2 particles and nanoscale roughness. Silicon-containing films find many applications for polymers, glass, ceramics & metals.
In the process, the product to be treated is fed through a laminar gas flame, doped with a silicon-containing precursor material (PYROSIL®), in a manner similar to traditional flame treatment. Reference Diagram 1. Due to the brief flame-substrate interaction the process can be used on temperature sensitive plastics materials. Combustion Chemical Vapor Deposition (CCVD) is a chemical process by which thin-film coatings are deposited onto substrates in the open atmosphere. In the CCVD process, a precursor compound is added to the burning gas. The flame is moved closely above the surface to be coated.
The high energy within the flame converts the precursors into highly reactive intermediates, which readily react with the substrate, forming a firmly adhering deposit. The microstructure and thickness of the deposited layer are controlled by process parameters including speed of substrate or flame, number of passes, substrate temperature and distance between flame and substrate. Silicon dioxide layers are the most commonly deposited layers. Freshly deposited layers are highly reactive and can thus serve as adhesion promoting layers for polymer coatings and bonding.
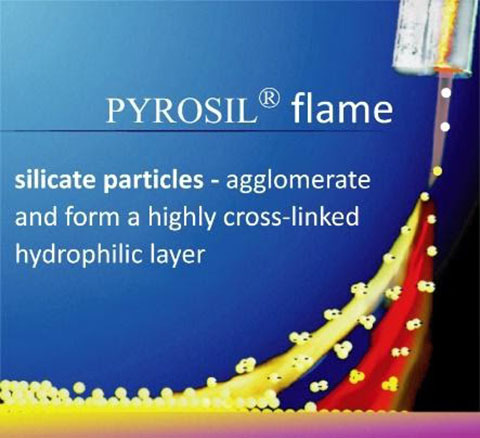
PYROSIL® Versus Flame Treatment
PYROSIL® and traditional flame plasma treatment have process similarities, but the flame chemistry and surface functionality mechanism are different. Reference Plastics Decorating Magazine Online- Flame Plasma Surface Modification of Polymers for Adhesion Bonding. Both methods are gas-phase surface oxidation processes in which the combustion of a hydrocarbon fuel, under controlled conditions, generates the flame plasma that modifies the substrate surface. Premixed laminar flames produce an exothermic reaction. The PYROSIL® flame is pinkish on color while the traditional flame treatment color is bluish in color. Reference Photo 1.
The main difference is that PYROSIL® produces SiO2 and flame treatment does not. Consequently, a defined hydrophilic surface is built due to the high density of Si–OH groups on the surface of the deposited SiO2 particles. Similar combustion equipment, ribbon burners and process setup/control are utilized.
The three main process control variables are flame chemistry, distance of the substrate from the flame and dwell time of treatment. Treatment must take place in the main reaction luminous zone or oxidizing.
For PYROSIL®, one equation for the combustion of organosilicon compound tetramethysilane “TMS” and the formation of SiO2 is:
Si(CH3)4 + 13 O2 + C3H8 —- SiO2 + 10 H2O + 7 CO2
For natural gas flame treatment, the following equation describes the combustion reaction:
CH4 + 2O2 + 8N2 —- CO2 + 2H2O + 8N2
Both combustion reactions produce CO? and H?O water byproducts.
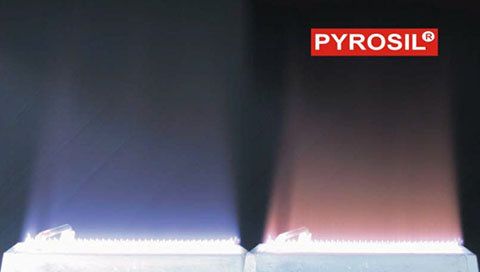
PYROSIL® Versus Cold-Gas Plasma
Prior to the invention of PYROSIL®, one of the most practiced methods for SiO2 thin-film deposition is PECVD (Plasma-Enhanced Chemical Vapor Deposition) which is performed in remote chambers under vacuum – low pressure glow discharge plasma. As the name implies the process is a chemical vapor deposition versus CCVD, a combustion vapor deposition. PECVD is conducted at lower temperature than standard Chemical Vapor Deposition and more versatile in producing many different types of film deposition coatings and functionalized surfaces. The major drawbacks are offline batch operations and high equipment/consumable costs. PYROSIL® is conducted at ambient conditions, ideal for cost effective inline operations. Reference Cold Gas Plasma Surface Modification.
Research Study: Bonding of Low Surface Energy Thermoplastics
There are extensive research studies documenting the PYROSIL® process. One study conducted by V. Seitz et.al compares atmospheric pressure plasma jet (APPJ) and a PYROSIL® flame for improved bonded strength on thermoplastics polybutylene terephthalate (PBT), polyetheretherketone (PEEK) and polyphenylene sulfide (PPS)2. This study explains lower contact angles were achieved using PYROSIL® and verified with photoelectron spectroscopy (XPS), 90°– peel test data, and surface analysis.


Contact angle (CA) Measurement
Water contact angles were measured on reference samples and after different surface treatments, shown in Fig. 3. The untreated thermoplastics exhibited a mainly hydrophobic behavior, as measured contact angles ranged between 86.2° (PBT) and104.0° (PPS). Plasma treatment as well as the PYROSIL® flame had a significant influence on the wetting behavior of all tested thermo-plastics leading to a clear decrease of the contact angle. For PBT, the contact angle decreased to 29.0° (plasma) and 10.1° (PYROSIL®). The hydrophilization of PEEK surfaces (reference 91.6°) was even higher resulting in water contact angles of 17.7° (plasma) and10.5° (PYROSIL®). For PPS, which offers the highest contact angles of the tested polymers, contact angles of 30.3° after atmospheric plasma treatment and 24.0° after the PYROSIL® flame treatment were measured.
The contact angle measurement confirms a hydrophilization of the thermoplastic surfaces by APPJ and the PYROSIL® flame as a significant decrease in water contact angle occurs. This improvement in wetting behavior is induced by the formation of functional groups on the polymer surface. The plasma treatment utilizes ambient air as a process gas, so oxygen and nitrogen containing groups are created on the surface. These polar groups improve the wetting behavior by water and, thus, the contact angle decreases. The PYROSIL® flame produces a thin SiOx-layer of some nm thickness on the polymer surface. The very good wetting behavior of this layer with contact angles between 10.1° (PBT) and 24.0° (PPS) indicates the formation of a high amount of hydrophilic silanol groups, which have a very high polarity compared to the nonpolar thermoplastics.
The XPS survey spectrum of PYROSIL® treated PEEK samples shows appearance of the Si2s and Si2p peaks, which is evidence for the deposition of a silica-containing layer on the thermoplastic surface, as untreated samples do not show these peaks. On PPS surfaces, a clear increase in Si can be observed on the PYROSIL® samples compared to the reference sample. Moreover, a remark-able increase of oxygen can be observed on both PEEK and PPS PYROSIL® treated surfaces, which is also a result of SiOx deposition.
Atomic Force Microscopy (AFM) Photo 2 shows SiO2 deposition layer which increases mechanical adhesion via micro-texture ³.
Manufacturing Application Considerations
The PYROSIL® technology, equipment systems and gas consumables are sold by Applied Surface Technologies LLC, the exclusive North American distributor of SURA Instruments GmbH. Custom design equipment is also available from other third party integrators. Among integrators, there are significant differences in experience and design of the combustion system, burner selection, zero gas pressure regulators, process control and surface testing. All equipment is not created equal!
The PYROSIL® name is sometimes loosely referenced by third party companies using near similar nomenclature but not the identical process. Such occurrences can create confusion to prospective buyers.
Different from PYROSIL®, another treatment method is a combination of flame treatment (for rapid heating) followed by spray atomized chemical primers. Sometimes the primer may contain SiOx species. This method is not CCVD.
For optimal PYROSIL® process results, carefully evaluate all equipment system components especially the combustion system design. Consider the following suggestions:
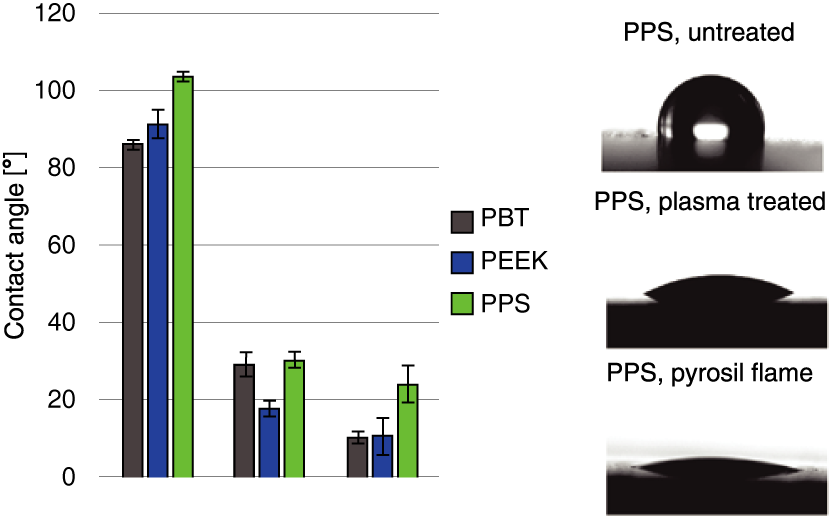
- Contact AST, SURA Instruments or a PYROSIL® CCVD expert at the beginning of a project to determine the required firepower (air output, burner capacity & length, air/gas mixture BTU’s), flame distance (flat or contoured geometries), optimal treatment level, precursor concentration, and equipment design.
- Properly analyze PYROSIL® treated surfaces to accurately determine polarity and the “receding” contact angle using ballistic deposition. Perform XPS testing to quantify O2 & SiO2 elemental composition (not an expensive test). Dyne solution testing alone does not provide the requisite information.
- Provide an engineering specification to potential equipment manufacturers and verify conformance before ordering equipment.
- Main consistent PYROSIL® process setup during manufacturing for repeatable adhesion results.
Conclusion
PYROSIL® is an excellent process for improving adhesion on polymers, glass & metals. It is well suited for treating large, molded surface areas with contours and flat blown films. Automated systems are highly effective and easily integrated. Unlike other gas-phase surface oxidation methods, PYROSIL® (CCVD) is a chemical process by which thin-film SiO2 coatings are deposited onto substrates in the open atmosphere.
PYROSIL® and traditional flame treatment have process similarities, but the flame chemistry and surface functionality mechanism are different. Combustion system design including all components is critical for optimal treatment. Minimal setup changes can result in adhesion bonding results. It is important to state that although generally valid, the concepts outlined in this paper may not apply in every application. Some aspects may require individual examination.
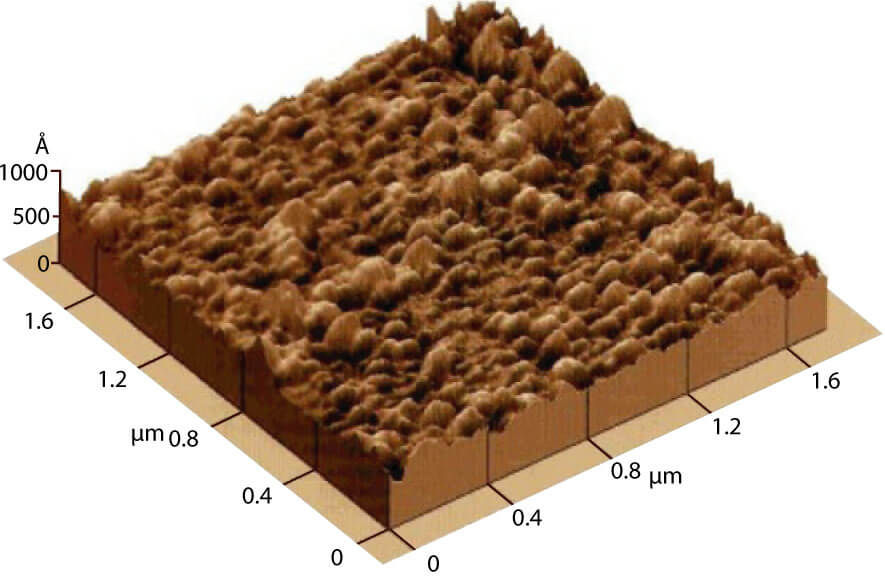
References
- Sabreen S. Flame plasma surface modification of polymers for adhesion bonding: process control, equipment and applications. Plastics Decorating Magazine July/August 2020.
- Seitz V, K. Arzt, Mahnel S, Rapp C, Schwaminger S, Hoffstetter M, Wintermantel E, (2015). Improvement of adhesion strength of self-adhesive silicone rubber on thermoplastic substrates – comparison of an atmospheric pressure plasma jet and a PYROSIL® International Journal of Adhesion & Adhesives, Volume 66.
- AST/SURA Instruments PYROSIL® A technology with a broad range of applications 2004.
Need Solutions to Surface Pretreatment & Adhesion Bonding Questions, call SABREEN (972) 820-6777
The Sabreen Group, Inc., is an engineering consulting company specializing in secondary plastics manufacturing processes – surface pretreatments, adhesion bonding, decorating & finishing, laser marking/laser welding and product security. SABREEN has been developing new technologies and solving manufacturing problems for over 30 years. Contact us 972-820-6777 or visit www.SABREEN.com.