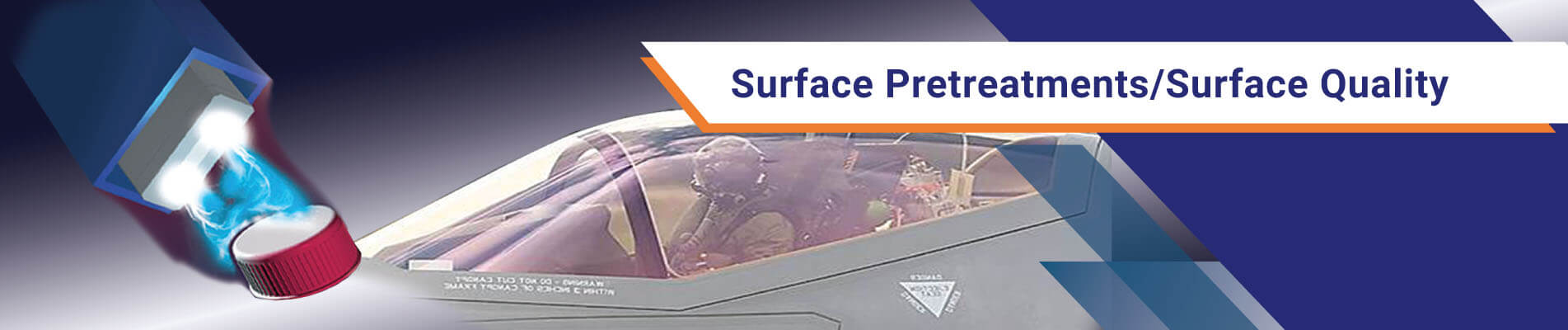
Flame Plasma
Flame treatment is a gas-phase pretreatment method in which the combustion of a hydrocarbon fuel, under controlled conditions, generates the flame plasma that modifies the substrate surface without affecting the bulk properties of the polymer. The oxidation of the polymer surface as a result of flame treatment occurs through multiple physical processes, including homogeneous combustion of the premixed reactants, transport of the products of combustion to the polymer surface and heterogeneous reaction of flame products with the polymer. The adiabatic flame temperature is approximately 3,300°F (1,816°C). The mechanism of flame treatment is the controlled combustion of a hydrocarbon fuel to generate the flame plasma. Premixed laminar flames produce an exothermic reaction. The exact ratio of oxidizer to fuel needed for complete combustion is known as the stoichiometric ratio. At stoichiometric combustion there is no excess oxygen or fuel. The stoichiometric ratio is approximately 10:1 for natural gas and 24:1 for propane.
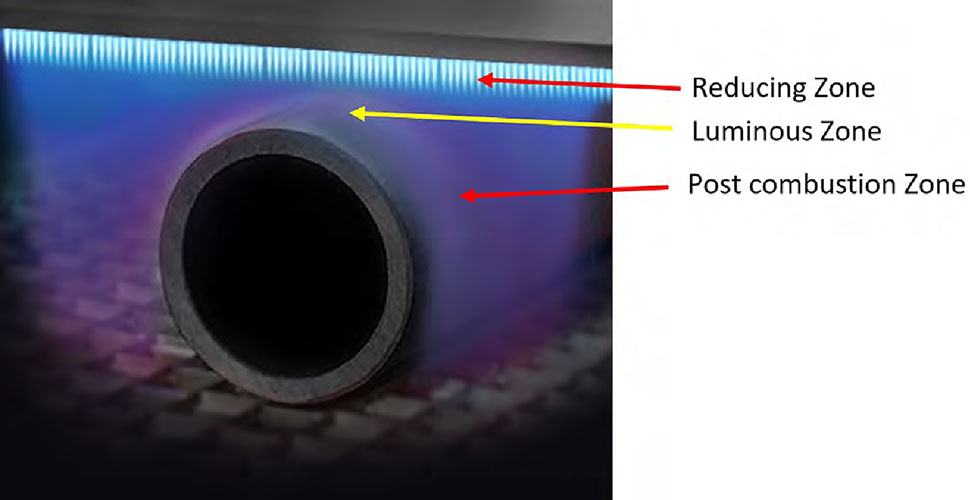
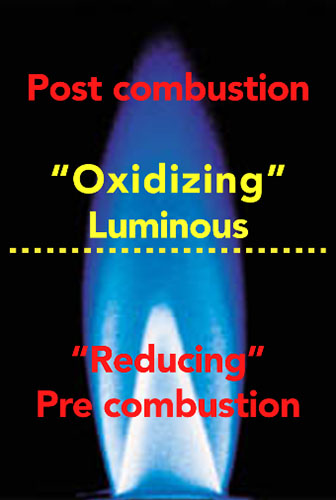
The flame is a mixture of a fuel and an oxidizer thoroughly mixed before combustion. The molar ratio of the fuel to the oxidizer is probably the most important parameter within the flame treatment process. For natural gas, the following equation describes the combustion reaction:
CH4 + 2O2 + 8N2 ? CO2 + 2H20 + 8N2 + flame plasma
The three main process control variables are flame chemistry, distance of the substrate from the flame and dwell time of treatment. In a combustion system the flame is a subsonic wave characterized by a velocity called laminar flame speed, which is defined as the velocity at which unburned gases move throughout the combustion wave in the direction normal to the wave surface. A laminar flame profile consists of three zones – reducing, luminous and post-combustion. Each zone has different temperature gradients and chemical reactive species. Placement of the part moving through the flame is critical and must be precise for maximum surface wetting and functionalization.
Optimal treatment (oxidation) occurs in the main reaction luminous zone or oxidizing. This is the hottest flame region, where temperature of the combustion system reaches approximately 1,700°C for natural gas and 1,900 to 2,000°C for propane-based mixtures. In this zone, free radical reactive species content (including hydroxyl, carbonyl, carboxyl, ether and ester) increases dramatically to the detriment of the reactant concentration. The high concentration of radical species makes this region strongly oxidizing, in contrast to the reducing zone.
The color of this zone depends on the fuel/air ratio. A deep bluish violet radiation, with the flame becoming almost transparent if the quantity of gas is increasingly reduced, is produced when the mixture is gas-lean (due to excited CH radicals). A green radiation appears when the mixture is gas-rich (due to excited C2 molecules). When the gas in the mixture increases still further, the radiation turns yellowish because of the carbon particles formed. Ideal flame chemistry is that which provides for an oxygen concentration in the flame plasma that is, after the combustion reaction, of 0.1% to 0.5%.
The optimal treatment distance (position) of the substrate from the flame (just above the pre-combustion reducing zone) is typically between 3/8″ and ½” (9.5 mm to 12.7 mm). The actual treating portion of the flame extends approximately 1½” (38.1 mm) beyond the flame tip, with about ½” (12.7 mm) producing the highest level of treatment. Reference the yellow dotted line in Diagram 1. The surface to be treated should never contact the reducing zone (sub-stoichiometric) of the flame.
The pre-combustion or reducing zone is the coldest region in the flame, where the premixed unburned gases have not reached the optimal oxidizing condition. Characterized by its bright steel-blue color, this region is ineffective for surface activation and offers no oxidation benefits. The post-combustion zone is the largest of the three regions in a laminar flame profile. The temperature remains high due to the exothermic oxidation reaction of CO into CO2, with a release of heat.
This region is characterized as intermediate, between reducing and luminous zones, in terms of temperature and oxygen radicals concentration. The high temperature burned gases generally present a reddish color, given by water vapor and carbon dioxide (combustion products with hydrocarbon combustibles) radiation and some dirt particles.
The gap (distance) between the luminous flame and substrate surface is a critical factor in determining the extent of activation accomplished by the treatment. Generally, when the substrate passes through the flame, a rapid depletion in the wettability of the treated surface occurs as the distance increases between the cones of the flame and substrate. However, a beneficial effect arising from the treatment is still appreciable several millimeters beyond the post-combustion zone. To maximize the benefit from the treatment, the flame should work in tandem with its luminous zone, which is the richest in active oxidizing species (OH radicals and O atoms) and the one at the highest temperature within the whole combustion system.
Zero gas pressure regulators should be installed with premix burner systems, using venturi air/fuel mixers to maintain a constant air/fuel ratio regardless of the burner firing rate. The venturi mixer is a proportional mixing device that has inlets for both the fuel gas (natural or propane) and air/oxygen, and inside the body mixes these gases properly and distributes them through the outlet. Functionally, as combustion air flows through the orifice in the air/fuel mixer, it causes a pressure drop that is sensed internally as a negative pressure through a downstream sensing tube in the zero gas pressure regulator – to maintain zero pressure relative to atmosphere.
Proper selection of burner type is critical to the uniformity and totality of treatment. Product design, geometry and polymer substrate are important factors. A well-designed burner will have a high level of stability, reducing the occurrence of flashback and flame lift, which are two types of instabilities that occur due to an imbalance between the fuel/oxidizer mixture flow velocity and the burn velocity of the combustible mixture. Flashback can develop in a premixed burner if the burning velocity of the flame exceeds the stream velocity flowing out of the port. Under these conditions, the maximum port diameter ensuring necessary thermal losses has been exceeded, thus allowing the flame to propagate back into the mixing chamber.
Two types of burners are used for flame treating: ribbon and drilled port. Ribbon burners consist of a series of crimped stainless steel ribbons inserted into brass, stainless steel, mild steel and cast iron. The number of ribbons, the crimp pattern and number of burner ports and other ribbon pattern design features depend on the application. Ribbon burners can offer advantages because of their ability to provide large flame surface and flame stabilization. The second type of burner is the drilled port. Drilled port burners are normally manufactured in stainless steel and aluminum.
Ribbon burners are the latest generation of burners and most widely adopted solution at an industrial level because the flame patterns are customizable by adjusting the width of the slot and configuring the ribbons3. Ribbon burners are the optimal solution for the surface modification or flame treatment of polymer films.