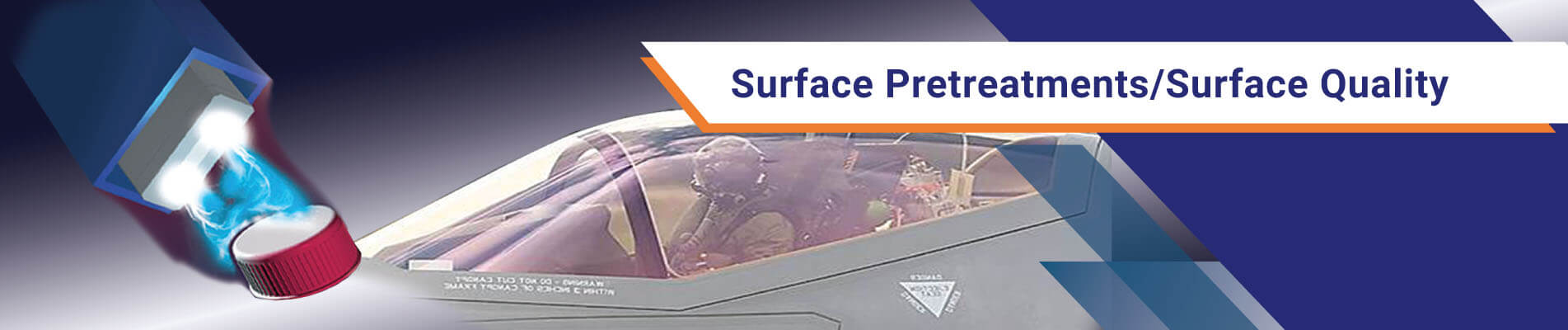
Pyrosil Flame Plasma
PYROSIL treatment is a combustion chemical vapor deposition (CCVD) process utilized to improve adhesion on surfaces to be bonded. PYROSIL is a glow-discharge plasma process conducted at ambient conditions. PYROSIL treatment is a surface modification technique that deposits an amorphous silicon dioxide (SiO2) layer on a substrate surface via Combustion Chemical Vapor Deposition (CCVD). SURA Instruments GmbH developed the equipment and processes in the 1980’s that lead to the first successful commercialization of the technology used to increase bonding with adhesives. By means of flame-pyrolysis, a thin layer (5 – 100 nm) of highly reactive and hydrophobic silicone oxide can be achieved on the substrate. Consequently, a defined hydrophilic surface is built due to the high density of Si-OH groups on the surface of the deposited SiO2 particles and nanoscale roughness. Silicon-containing films find many applications for polymers, glass, ceramics & metals. In the process, the product to be treated is fed through a laminar gas flame, doped with a silicon-containing precursor material (PYROSIL), in a manner similar to traditional flame treatment. Due to the brief flame-substrate interaction the process can be used on temperature sensitive plastics materials.
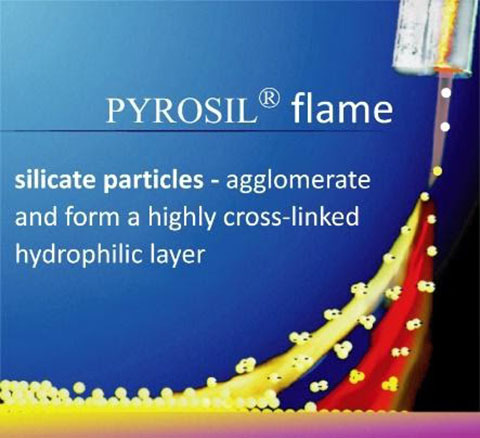
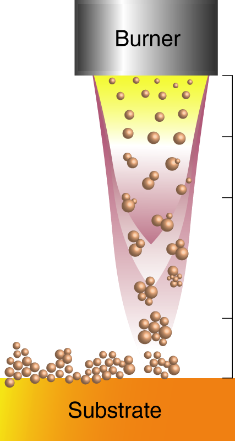
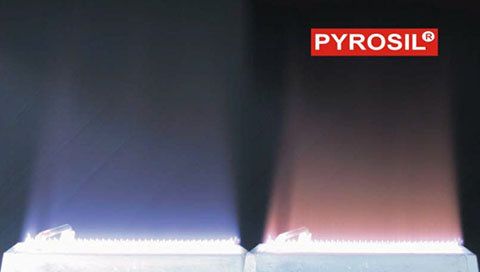
Combustion Chemical Vapor Deposition (CCVD) is a chemical process by which thin-film coatings are deposited onto substrates in the open atmosphere. In the CCVD process, a precursor compound is added to the burning gas. The flame is moved closely above the surface to be coated. The high energy within the flame converts the precursors into highly reactive intermediates, which readily react with the substrate, forming a firmly adhering deposit. The microstructure and thickness of the deposited layer are controlled by process parameters including speed of substrate or flame, number of passes, substrate temperature and distance between flame and substrate. Silicon dioxide layers are the most commonly deposited layers. Freshly deposited layers are highly reactive and can thus serve as adhesion promoting layers for polymer coatings and bonding.
PYROSIL Versus Flame Treatment
PYROSIL and traditional flame plasma treatment have process similarities, but the flame chemistry and surface functionality mechanism are different. Both methods are gas-phase surface oxidation processes in which the combustion of a hydrocarbon fuel, under controlled conditions, generates the flame plasma that modifies the substrate surface. Premixed laminar flames produce an exothermic reaction. The PYROSIL flame is pinkish on color while the traditional flame treatment color is bluish in color. Reference Photo 1. The main difference is that PYROSIL produces SiO2 and flame treatment does not. Consequently, a defined hydrophilic surface is built due to the high density of Si–OH groups on the surface of the deposited SiO2 particles. Similar combustion equipment, ribbon burners and process setup/control are utilized. The three main process control variables are flame chemistry, distance of the substrate from the flame and dwell time of treatment. Treatment must take place in the main reaction luminous zone or oxidizing.
For PYROSIL, one equation for the combustion of organosilicon compound tetramethysilane “TMS” and the formation of SiO2 is:
Si(CH3)4 + 13 O2 + C3H8 — SiO2 + 10 H2O + 7 CO2
For natural gas flame treatment, the following equation describes the combustion reaction:
CH4 + 2O2 + 8N2 — CO2 + 2H2O + 8N2
Both combustion reactions produce CO2 and H2O water byproducts.