Plasma Surface Pretreatment
Plasma Surface Treatment of Plastics
Plasma Pretreatment Improves Polymer Adhesion
Plasma surface pretreatments, specifically termed as “gas-phase, glow-discharge” plasma surface oxidation, can resolve adhesion bonding difficulties between low surface energy plastics and adhesives, coatings, printing inks, paints, and sealants. These methods include electrical corona, atmospheric plasma, electrical blown air plasma, flame plasma, Pyrosil, remote-cold gas plasma, and UV radiation ozone. All these processes are characterized by their ability to generate “gas plasma”. In the science of physics, the mechanisms by which these plasmas are generated differ, but their effects on surface wettability are similar. In addition to plasma treatment, there are other highly effective methods including chemical, Fluorooxidation, and mechanical.
The SABREEN Group was the first to patent corona plasma pretreatment of 3-dimensional polymer surfaces for military electronic devices (US505186, 1991). SABREEN’s over 40 years of hands-on experience in adhesion bonding, adhesives, surface science chemistry, surface pretreatments, bonding processes, adhesion failure modes, analytical testing, polymers, molding operations, and systems integration ensure robust bonding process excellence.
Applications include:
- Bonding plastics, composites, metals
- Plastic and metal coatings
- Inkjet printing
- Printing on polymer films
- Hydrophobic / hydrophilic coatings
- Microfluidic devices
- Coatings of plastic, glass, metals
- Teflon / PTFE
Adhesion Bonding & Plasma Pretreatment Experts
- Examine every process – Molding through Assembly
- Evaluate multiple plasma pretreatments (equipment onsite)
- Accurately measure critical process factors – ASTM standard
- Contact angle, surface energy
- Dishwasher testing
- Adhesion, cohesion, failure mode
- Curing & meter profiling
- Taber abrasion, scratch/mar
- Coating thickness wet/dry
- Chemical resistance
- Accelerated, UV aging
- Identify critical root-causal problems, solution validation
Implement 6-Sigma Process Solutions
Adhesion bonding is a “Process” – not just a machine. To understand the differences between plasma pretreatment methods, it is important to clarify any ambiguous terminology sometimes used by suppliers for marketing purposes. Equipment design, functionality, and plasma purity vary significantly between manufacturers which has a substantial impact on treatment quality, product performance, and shelf-life.
Common process application problems include:
- Technical training
- Adhesive selection
- Texture
- Parts storage
- Contaminated parts
- Chemical primer
- No hand protection
- Temperature and humidity
- Inconsistent pretreatment
- Mixing
- Viscosity
- Wet/dry-film thickness
- Clamping pressure
- Curing recipe
- Oven curing
- QC
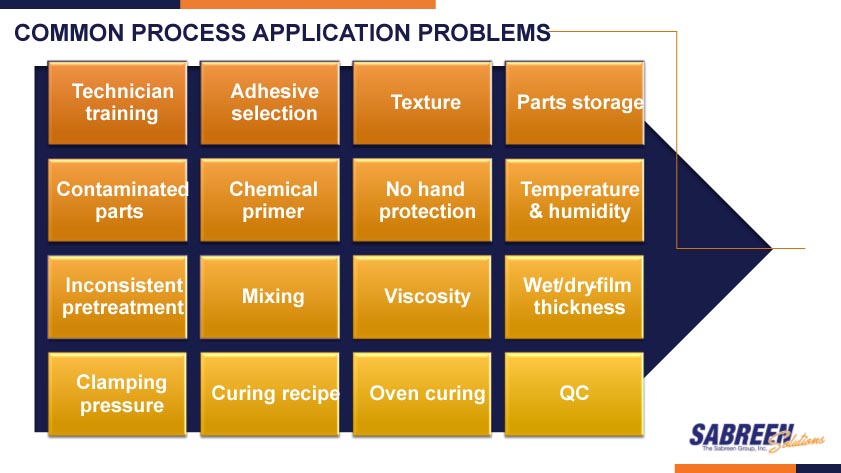
Let SABREEN’s Expertise Benefit Your Company
Why are Plastics Difficult to Bond?
Plastics and composites are difficult to bond because their surfaces are hydrophobic, non-polar, chemically inert, and have low surface energy. Adhesion occurs via multiple mechanisms involving mechanical interlocking, molecular diffusion, electrostatic interaction, wetting, chemical bonding, and the formation of a weak boundary layer, all of which occur simultaneously. The degree of the bond strength achieved is determined by both the properties of the two materials and the bonding/joining process. For achieving optimum adhesion, the adhesive (coating, ink, or paint) must thoroughly “wet out” the surface (adherend) to be bonded.
Featured Webinar by Scott Sabreen
In this recorded webinar, you will gain a better understanding of the science behind surface pretreatment of different plastics and learn how to determine the best solutions for your adhesion challenges.
Topics covered:
- Adhesion versus cohesion failure
- Why pretreatments are required for low-energy plastic substrates
- Effects on adhesion from primary molding operations
- How to select the best pretreatment process
- Diagnostics, trouble-shooting and solutions
- “Best Practices” manufacturing process methods
- Real-life case studies
Why is Surface Pretreatment Necessary?
Plastics materials possess low surface energy and low interfacial adhesion properties when bonding adhesives, coatings, inks and paints. Plasma surface pretreatments are used to promote adhesion between difficult-to-bond plastic substrates and “Gas-phase” plasma surface (modification) oxidation is the most common modification method and is proven to be highly effective, economical and environmentally safe. The selection of which method to utilize on any given application can be challenging. Through understanding the basic science of contact angles, surface wetting and chemical activation, virtually all bonding problems can be solved, even when using the most tough-to-bond polymeric and elastomeric materials.
What is “Gas-phase” Plasma Surface (Modification) Oxidation?
Which plasma process is best for your application? Click on the buttons below to learn about each method.
Hydrophilic Surface
Hydrophobic Surface
Partial Wetting
The contact angle is the angle, typically measured through the liquid, where a liquid-vapor interface meets a solid interface. The contact angle quantifies the wettability of a solid surface by a liquid via the Young equation.
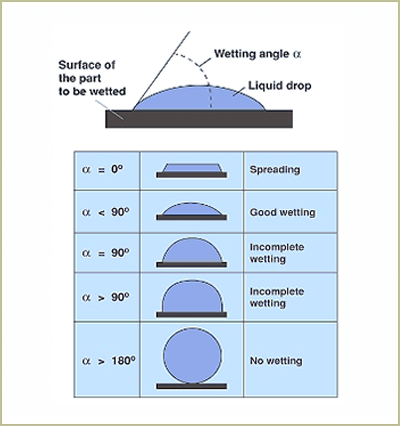
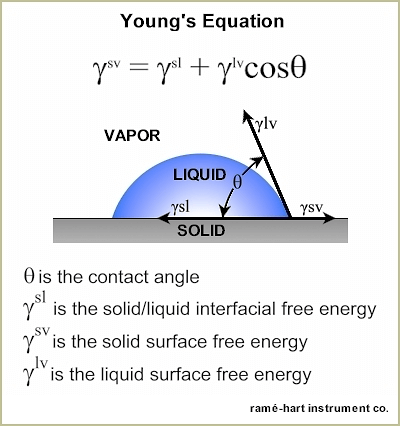
Testing the fluid behavior of only the static contact angle can lead to misinterpretation of the liquid/solid interface results and the resolution of bonding problems. This is because industrial manufacturing production operations are more realistically dynamic conditions, not static. Thus, the dynamic contact angle (DCA) is important to understand. Contact angles generally are affected by both changes in surface chemistry and changes in surface topography.
The advancing contact angle is most sensitive to the low-energy (unmodified) components of the substrate surface, while the receding angle is more sensitive to the high-energy, oxidized groups introduced by surface pretreatments. Thus, the receding angle is the measurement most characteristic of the modified component of the surface following pretreatments, as measured using dyne solutions. Therefore, it is important to measure both the advancing and receding contact angles on all surface-modified materials.
When a droplet is attached to a solid surface, and the solid surface is tilted, the droplet will lunge forward and slide downward. The angles formed are respectively termed the advancing angle (θa) and the receding angle (θr). ASTM D724 describes methods for measuring DCAs using advanced equipment (optical tensiometers and goniometers) to analyze advancing and receding contact angles based on drop shape analysis and mass.
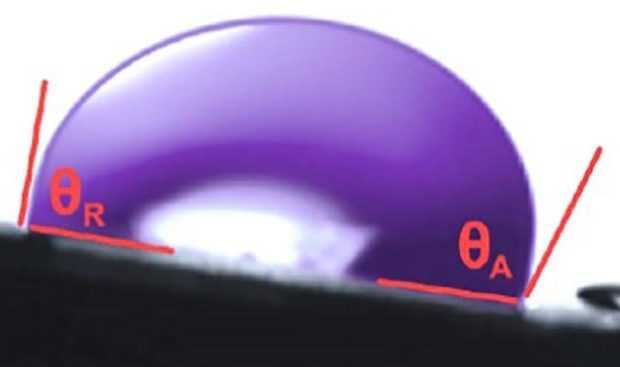
The underlying reasons why many plastics are difficult to bond are because they are hydrophobic non-polar materials, chemically inert and possess poor surface wettability – i.e., low surface energy. While these hydrophobic (repel water) performance properties are ideal for part designers who seek such properties, they are the nemesis for manufacturers needing to bond such materials. Robust adhesion bonding usually necessitates “hydrophilic” surfaces. For optimum adhesion to occur, an adhesive (coating, ink or paint) must thoroughly “wet out” the surface (adherend) to be bonded.
“Wetting out” means the liquid flows and covers a surface to maximize the contact area and the attractive forces between the adhesive and adherend bonding surface. For a liquid to effectively wet out a surface, the surface energy of the adhesive must be as low or lower than the surface energy of the adherend to be bonded. Alternatively, the surface energy of the substrate must be raised.
Consider a single liquid fluid droplet on a flat solid surface at rest (equilibrium). The angle formed by the solid surface and the tangent line to the upper surface at the end-point is called the contact angle; it is the angle (?) through the liquid between the tangent line at the contact point and the horizontal line of the solid surface. The bubble/droplet shape is due to the molecular forces by which all liquids, through contraction of the surface, tend to form the contained volume into a shape having the least surface area. The intermolecular forces that contract the surface are termed “surface tension.” Surface tension, a measurement of surface energy, is expressed in dynes/cm (SI N/m).
The higher the surface energy of the solid substrate relative to the surface tension of a liquid (water, printing inks, adhesives/encapsulation, coatings, etc.), the better will be its “wettability” and the smaller will be the contact angle (Figure 1 on page 2). As a rule, acceptable bonding adhesion is achieved when the surface energy of a substrate is approximately 8 to 10 dynes/cm greater than the surface tension of the liquid.
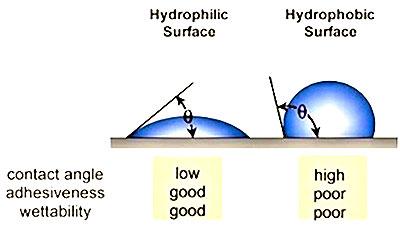
For many applications, it may only be necessary to examine the static equilibrium contact angle using dyne solutions in accordance with a documented test procedure. Application kits or “dyne pens/solutions” provide useful information, but they are not precise measurements of surface tension. Surface tension measurements can vary considerably by individual (technique) and the interpretation of the “center” liquid behavior. Dyne pens/solutions are known to be directional indicators of significant differences in the surface tension and are capable of identifying “good” and “bad” bondable surfaces at economical pricing. Bottled dyne solutions can be preferable to pens because of contamination issues due to multiple uses.
Best method for inspecting surface quality:
The Surface Analyst™ 2001 is a handheld digital device for measuring contact angles in-line production without using chemical dyne solutions. The method is nondestructive; thus the part can be processed as usual – unlike dyne solution testing in which the part is scraped. Invented by BTG Labs, the Surface Analyst™ was engineered to put precision surface measurement technology in the hands of shop-floor technicians for operations where surface condition is critically important, such as adhesive bonding, painting, coating, printing and decontamination. Using a patented technique called “ballistic deposition,” the device deposits a highly purified drop of water on the substrate surface.
By knowing the volume and area of a drop of water, the device then calculates the contact angle of the water against a given surface. The device provides immediate feedback to the user with a quantifiable number or a Pass/Fail alert. The inspection data provided by the device allows users to determine if the substrate has been properly prepared for adhesion processes, as a replacement for destructive dyne solutions. The handheld unit operates in any orientation and works on smooth or textured surfaces, such as grained TPOs. This data can be used for continuous process improvement, identifying quality drifts that may signal imminent problems or to pinpoint the critical cause of product failures.
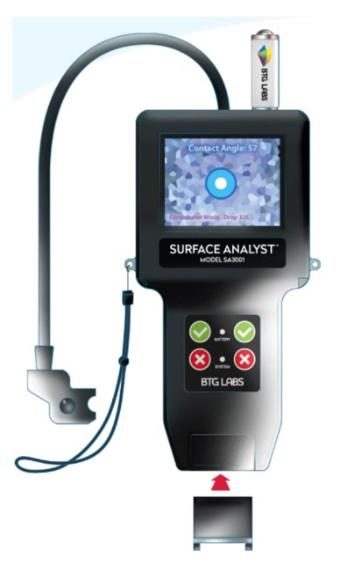
There is a strong tendency for manufacturers to focus only on contact angles or other wettability measurements as the sole predictor for bonding problems and for conducting routine surface testing. Chemical surface functionality is equally important, whereby hydrophobic surfaces are activated into bondable hydrophilic surfaces. Gas-phase, “glow-discharge,” surface oxidation pretreatment processes are used for chemical surface activation. These processes are characterized by their ability to generate “gas plasma,” an extremely reactive gas consisting of free electrons, positive ions and other species. Plasmas often can be described as a fourth state of matter. As energy is supplied, solids melt into liquids, liquids vaporize into gases, and gases ionize into “plasmas.”
In the science of physics, the mechanisms in which these plasmas are generated are different, but their effects on surface wettability are similar. The basic chemical and physical reaction that occurs is free electrons, ions, metastables, radicals, and UV generated in the plasma can impact a surface with energies sufficient to break the molecular bonds on the surface of most polymeric substrates. This creates very reactive free radicals on the polymer surface that, in turn, can form, cross-link, or in the presence of oxygen, react rapidly to form various chemical functional groups on the substrate surface. Polar functional groups that can form and enhance bondability include carbonyl (C=O), carboxyl (HOOC), hydroperoxide (HOO-), and hydroxyl (HO-) groups. Even small amounts of reactive functional groups incorporated into polymers can be highly beneficial to improving surface chemical functionality and wettability. Also, chemical primers/solvents and mechanical abrasion (including mold tool texture) can be utilized alone or in conjunction with pretreatments.
The degree or quality of pretreatment for robust adhesion strength is affected by the cleanliness of the plastic surfaces. The surface must be clean to achieve optimal pretreatment and subsequent adhesion. Contamination sources on product surfaces that inhibit treatment includes dirt, dust, grease and oil. Low molecular weight materials such as silicones, mold release and anti-slip agents are particularly deleterious for bonding. Material purity is also an important factor. Further, certain soluble or nonsoluble compound agents used in pigment and dye colorants can adversely affect adhesion.
The shelf life (treatment aging degradation) of treated plastics depends on the type of resin, formulation and the ambient environment of the storage area. Shelf life of treated products is limited by the presence of low molecular weight oxidized materials (LMWOM) such as antioxidants, plasticizers, slip and antistatic agents, colorants and pigments, stabilizers, etc. Exposure of treated surfaces to elevated temperatures increases molecular chain mobility. The higher the chain mobility is, the faster the aging of the pretreatment. Plasma-treated surfaces age at different rates and to varying extents relative to factors with the surrounding environment. Aging characteristics and their storage shelf life are essential to manufacturing process operations. Activated surfaces may have a shelf life of hours, days, months or longer. It is recommended to bond, coat, paint or decorate products as soon as possible following pretreatment.
Recognize that each surface pretreatment method is application-specific and may possess unique advantages and potential limitations. For robust results, consider the following factors:
- Polymers react differently to oxidation processes. The type of polymeric substrate and its end-use performance requirements are critical in determining the selection of pretreatment method.
- Is the substrate (product to be treated) conductive? For example, unassembled plastic electronic connector bodies – without metal contact pins – can be treated electrically, whereas assembled connectors may experience electrical arcing problems.
- Part geometry – flat surfaces are more easily treated compared to deep recesses, extreme tapers, and other shape irregularities. Wetting tests are difficult to conduct in small areas and on heavily textured surfaces.
- Material handling automation: Conductive belts and chains may cause electrical arcing with classical electrical corona discharge and spot treaters. Alternatively, consider using flame, cold gas plasma, or low-potential atmospheric plasma.
- Avoid overtreatment. Excessive plasma-oxidized surfaces may deleteriously affect downstream assembly processes such as heat sealing/welding.
- All pretreatment equipment is not created equal. Examine the quality of constructed systems in action. For electrical treatment processes, observe the uniformity of the plasma discharge; for flame treatment, consider the differences between ribbon vs. drilled port burners and combustion system components; for cold gas plasma, examine the quality of the chamber construction, electrode shelves and particularly the manufacturer of the vacuum pump.
Surface roughness is the degree of unevenness of the surface of a solid below the scale of magnitude of its shape or undulation but above the irregularity of crystal lattice structures.
The degree of roughness affects the wettability of a solid. As roughness goes hand-in-hand with an enlarged surface area, it affects the wettability of a solid, the contact angle of a liquid, and the adhesion.
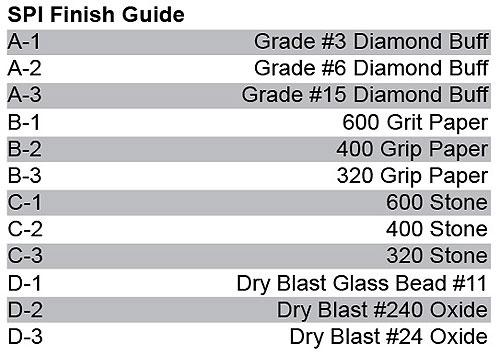
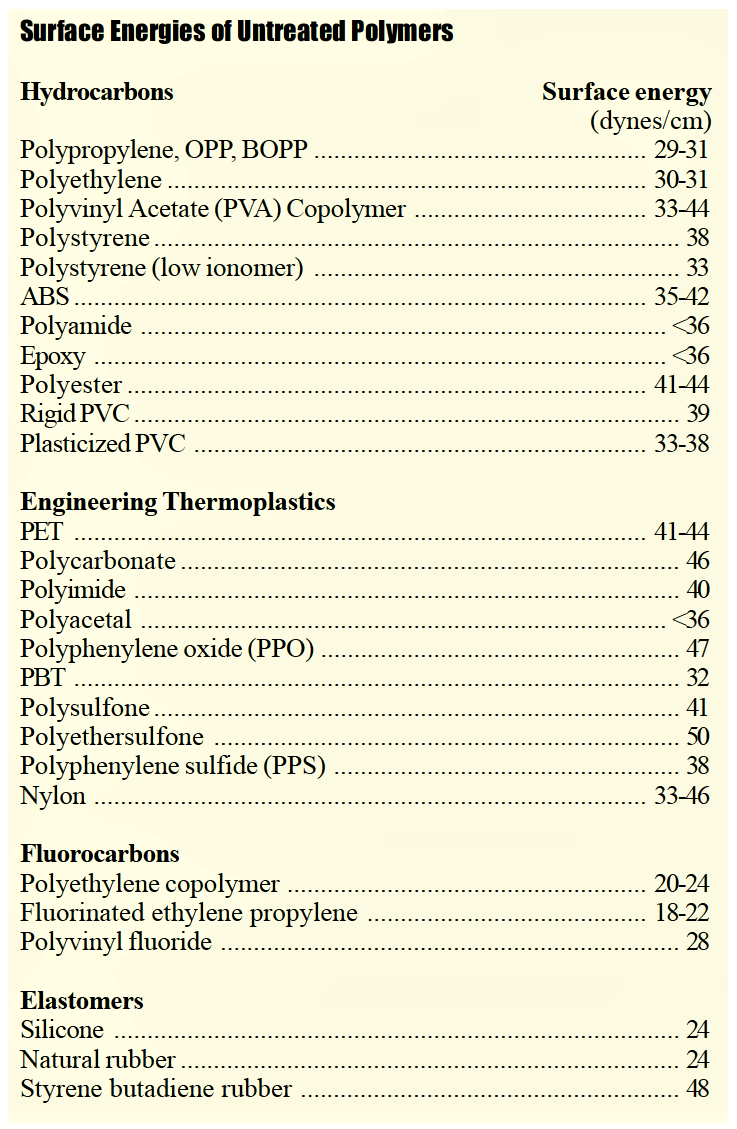
Surface Wetting Test Procedure Using Dyne Solutions
This procedure describes a method for testing and measuring the surface wetting tension (i.e. surface energy) of plastic substrates using dyne test marker pens.
Surface wetting tests should be conducted immediately after pretreatment (corona discharge, flame treatment, RF gas plasma). Treated surfaces are time sensitive and are affected by environmental conditions such as temperature and humidity. Substrates must have clean surfaces for optimal adhesion. Dirt, dust, hand/finger oils, silicone-based products, and other contaminates inhibit adhesion and can cause erroneous test results.
1.0 Materials / Equipment
- Dyne marker pens – levels available: 30, 32, 34, 36, 38, 40, 42, 44, 46, 48, 50, 52, 54, 56, 60
- Products to be tested
- Plastic gloves
- Chemwipes or paper towels
- Temperature and humidity gages
- Clean work area
2.0 Method
- Record ambient temperature and humidity.
- Select 60 dyne pen and remove the cap.
- Place the product to be tested on a flat surface and firmly press the marker pen applicator tip down onto the product until solution is drawn into the tip.
- Using a light touch, draw the pen across the length of the pretreated surface one time to apply a thin fluid layer.
- Parallel passes are recommended. Excessive solution will result in misreading.
- Note the time it takes for the liquid to break into droplets. The reading of the liquid behavior should be observed in the center of the liquid.
- If the liquid does not break into droplets after two (2) seconds, then the surface energy is assumed to be a minimum of 60 dynes. Proceed to step 2.7. If the liquid breaks into droplets in less than two (2) seconds, repeat the test using the next lower dyne marker pen. Adjustments to the pretreatment process may be necessary.
- The test is completed when all surfaces achieve the desired wetting results.
- Properly discard tested products.
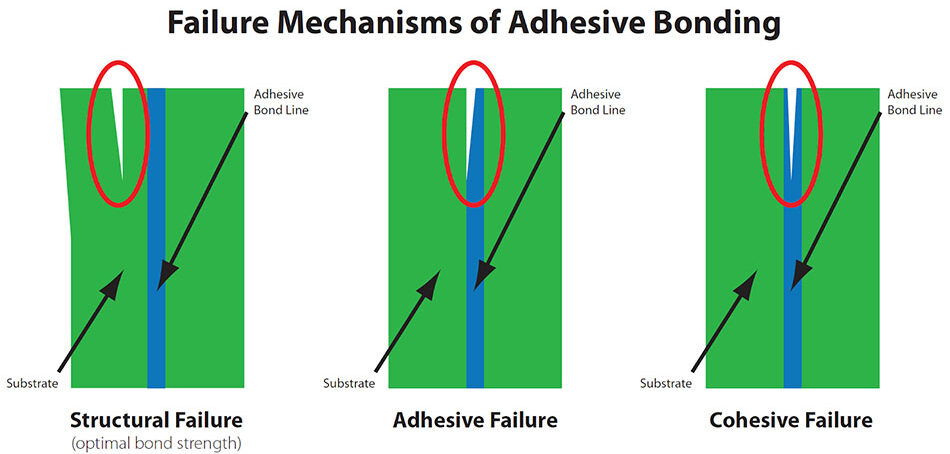